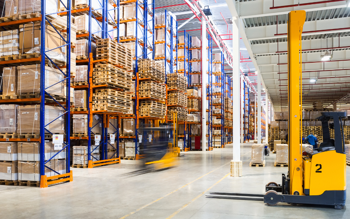
The aim of this article is to try and cut through the noise and provide you with a balanced and objective, as possible, view on the pro’s and con’s of robotics; and whether I predict it will be something worth investing in or a future flop.
Why should you trust my opinion; well, I’ve worked in the technology space for over 10 years, been pitched countless new technologies in that time and it’s been my role to determine whether they’re something I should be recommending to the companies I work for or not. Hopefully I can give enough insight to form your own opinion.
Is robotics really a new concept?
Robotics to automate tasks in supply chains is not a new concept. Many manufacturing environments implemented forms of warehouse robotics into their factories as an evolution of the industrial revolution that mechanised manual, repetitive tasks to increase productivity. So, although robotics being aimed towards the order fulfilment segment of supply chains is emerging, a lot of the pros and cons of their implementation can be gleaned by looking at the past.
What is warehouse robotics?
Before I dive into an exploration of what a look back at the past can teach us, let’s first align on what I’m including as ‘new’ robotics and the individual merits of each.
Warehouse robotics refers to the use of automated machines and robots to perform tasks within a warehouse or distribution centre, such as moving and organising inventory, picking and packing orders, and transporting goods. These robots are designed to improve efficiency, accuracy, and speed in warehouse operations.
The other is delivery robotics; automating the delivery of goods dispatched from the warehouse to the customer. I’m going to focus this article on the former; warehouse robotics but wanted to call out the other type so it’s clear I’m not completely ignoring them.
Types of warehouse robotics
This isn’t an exhaustive list but the common types I’ve experienced operating in warehouses are:
Automated Guided Vehicles (AGVs)
These are essentially self-driving forklifts that can be used to manage movement of goods safely in/out and around the warehouse. Still being a forklift, they are best suited to moving larger bulkier items such as pallets.
Pros
Easy to phase in
Most warehouse already use forklifts, so impact is minimal on existing operations and building layouts.
Reduced labour costs
Machines tend to cost over less over their lifetime than a human does to hire, train, and maintain their employment.
Increased safety
With no humans involved then there is no risk of human error; AGV’s also have far more safety systems built into them than their human powered equivalents.
Cons
High initial investment
Although over their lifetime they will be cheaper than buying normal forklifts and hiring staff to run them; the initial costs for AGVs are high. In short you need to have the capital available to be able to take a high year 1 cost in order to see the longer term cost benefits.
Less flexible
They’re designed to follow specific predetermined processes and complete only repetitive tasks. You can’t just grab one to handle a one-off task. This is great for some but those that operate in a more agile, flexible way will become unstuck quite quickly.
Autonomous Mobile Robots (AMRs)
These are robots that move around your warehouse to pick up and move items around your warehouse and there are a few ways in which they do this. Some pick up whole racks and move them to where the operator is for the operator to pick the item they want, these are called ‘goods-to-people’ AMRs. Whilst others follow the operator around with a basket for picked items to be placed in and taken to be packed. These are called zone picking AMRs and the warehouse must be divided into zones with operators staying within their allocated zone.
Pros
Increased flexibility
Unlike AGV’s that must follow set paths and processes; AMRs can create their own pathways between locations, learning the most efficient way to get from point A to point B. This also means that they can be switched to learn new tasks with relative ease.
Implementation ease and scalability
AMRs can be implemented with relative ease, particularly the zone picking versions; and once implemented scaling them is a case of buying more units and setting them to work. They’re also much easier to move between facilities than other types of robotics due to their ability to learn their own pathways.
Cons
Load size limitations
Although some AMRs can handle high weights, such as ‘goods to operator’ AMRs; they aren’t well suited to operations that would normally be handling goods with the use of forklifts.
High initial cost
As with all emerging technologies, they cost a lot. For you to get the return on the investment you need to be an medium to large operation that handles a high volume of SKU’s. This is because the primary benefit of AMRs is to increase productivity through reducing travel time. If you’re not shifting enough stock then the returns won’t be realised.
Implementation impact
I’m contradicting myself here a little bit, but bear with. If your warehouse is already designed to accommodate AMRs then implementation is easy; but if you're looking to implement ‘go-to-people’ AMRs then it’s likely there will be considerable downtime.
Static Robots
This type of robot is more akin to those you see in manufacturing; where they are fixed to the floor and carry out tasks from the confines of the location, they have been placed in. Their uses include packing, sorting and palletisation of stock.
Pros
Adaptability
Being a robotic arm that is programmed to carry out a task, they can easily be reprogrammed to adapt as your warehouses needs change. For example, changes to product lines or pallet shapes.
Efficiency
They’re able to learn and optimise the processes they have been programmed to do and so over time the productivity gains they can deliver will increase. They can also be combined with other automation systems, such as conveyor belt systems to fully automate your warehouse which means the efficiency of the systems and overall productivity improvements can continue to increase.
Cons
Impact on existing operations
Being static it is likely you would need to reconfigure your warehouse and processes to accommodate them. This will cause downtime and could cause inefficiencies in other areas as staff learn the new processes required to work with these robots.
Loss of flexibility
Although they can be adapted to carry out different tasks, the use cases for these robots is still quite limited and so when the high cost of investment is considered the lack of flexibility may limit their impact on your operations.
Automated Storage and Retrieval System (ASRS)
This is a fully automated system where robots can book in, sort, transfer, replenish, and pick stock. They can be programmed to carry out one or more of these tasks, with options to programme them to complete each task in multiple ways, e.g. taking a whole shelf, one tote / bin, or a single product to the operator during picking.
Pros
Highly flexible
Depending on the implementation you can get these robots to carry out almost any task within your warehouse, being modular too means you transition to full automation at your own pace.
Better use of space
Typically these systems don’t require aisles to be as wide, and because they’re able to go up and down quickly, you can start to utilise vertical space more as well. All of which means that you can get more utilisation from your existing warehouse space before having to invest into further building expansion.
Cons
High initial investment
All of these robotic implementations have a higher initial cost than their ‘manual’ counterparts, but ASRS costs can be particularly high when considering it’s likely you’d need to invest in not just the robotics but also the surrounding infrastructure to enable them to operate within your warehouse.
Are warehouse robotics worth the investment?
Robotics will not be right for every business, some businesses will not be processing enough stock to see any returns from investing in the technology, whilst others it will be so hard to retrofit them into their operations that the cost to do so will make it unpalatable.
The costs will reduce as more companies adopt but this is going to take time as the current prices will be a barrier for entry for many. The tipping point will be when enough companies have successfully implemented the technology.
The key factor in determining the success of an implementation will come down to how well the business planned for the technology before they bought it.
Advocates of robotics in warehousing will all downplay the disruption caused by a robotic implementation. However, disruption will be impossible to avoid. Creation of a detailed execution plan considering every part of your operation is a critical step, not an optional one.
Estimating business disruption
Think about how the roles of your people will change, which processes will need to be altered, and whether your warehouse can accommodate the technology easily or not. From this you can estimate the impact to your business. Worst case your whole operation will need to be shut down, best case people and processes need to adapt.
Not only will estimating disruption help an implementation go more smoothly, but it will also highlight the risk of investing in the technology before you’ve parted ways with your hard-earned cash. From this you’ll be in a great position to decide whether robotics are right for your business or not.
Will warehouse robotics survive ‘the chasm of uncertainty’?
I mentioned at the top of this article that we can take learnings from the past industrial revolutions. Ultimately the adoption of machines has been successful and robotics in many ways is just an evolution of this; so, I do expect this technology to gain traction.
I think the technology will survive and grow to wide scale adoption but the speed in which this happens will be determined by those who invest in it and how successfully they integrate the technology into their businesses.
I’ve seen some promising technologies fall into obsolescence because early adopters’ projects haven’t gone how they thought they would, word of mouth spreads and the technology is avoided like the plague.
Let’s hope this won’t be the fate of warehouse robotics.
The future of order fulfilment with Mintsoft
Knowing whether to adopt new technology, such as robotics can be difficult, many businesses begin by automating their existing processes. We’ve explored this topic separately in articles such as our guides to Warehouse Technologies and the Future of Fulfillment and the Benefits of Warehouse Automation.
If you’d like to explore the Mintsoft platform further, please book a call with one of our product experts, or learn more about our warehouse management software.