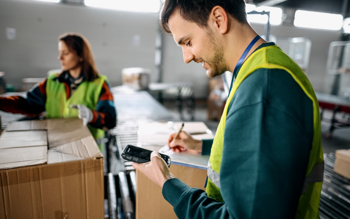
- What is the FIFO method, and what does it stand for?
- How FIFO works in warehouses
- Advantages and drawbacks of FIFO inventory management
- FIFO vs FEFO, which is better?
- Tips for implementing FIFO stock management in your warehouse
- Track product entry and exit dates for FIFO with Mintsoft’s inventory management software
What is the FIFO method, and what does it stand for?
The FIFO method stands for First In, First Out (FIFO). It is one of the most common inventory management methods for organising and managing inventory. It focuses on the first stock item to enter your system, being the first one to be processed and pushed out.
FIFO is also used in accounting to place a monetary value on your inventory and calculate the cost of goods sold (COGS). In accounting, FIFO assumes the most recently purchased inventory is sold last because your first batch will be sold first.
Calculating your COGS will take the first inventory you purchased and assign it to the cost of goods.
FIFO is most commonly used in industries that produce perishable goods or products with a fixed shelf life and expiration date. For example, the grocery industry uses FIFO to push out products with an expiration date first, and a cosmetic brand uses FIFO to ensure that the first inventory batch is sold first.
How FIFO works in warehouses
A FIFO method is an inventory management system that helps you get higher profits, keep efficient stock on rotation, and maximise your warehouse space.
Step 1: Inventory Receipt
When your new batch of inventory is received, it is placed at the end of the line in storage, pushing the older stock in the front, ready to be pushed out first.
Inventory Receipt Example:
Let’s say your warehouse receives the following inventory:
- 100 units of Product X (Inventory Batch 1) at $10 each, received on 1st January.
- 150 units of Product X (Inventory Batch 2) at $12 each, received on 1st March.
FIFO Placement Example:
- The 100 units from Inventory Batch 1 (the first to be received) are placed in the front to ensure they are the first to be picked when fulfilled.
- The 150 units from Inventory Batch 2 are placed behind Inventory Batch 1.
Step 2: Inventory Organization
Every batch of your inventory should be organised with the date it was received, price, and stock quantity. This will ensure your staff and team can select the correct batch for distribution.
For the FIFO method to be effective, you must organise the items chronologically so your team can easily identify the oldest received batch in the fulfillment process.
You can track your inventory using labels or barcodes through an inventory management software.
Step 3: Order Fulfillment
This step lets you see if your FIFO method system is working. Your staff should ensure the oldest stock is selected when placing orders.
Order fulfillment in the FIFO method example:
Let's say customer A orders 50 units of Product X.
According to the FIFO system:
- The first 50 units picked will be from Inventory Batch 1 (received 1st January) because they are the oldest inventory batch.
- The next 50 units picked will come from the rest of Inventory Batch 1, followed by Inventory Batch 2.
Step 4: Inventory Replenishment
As the cycle continues and your warehouse stock is depleted, you must replenish it. As new inventory comes into your warehouse, you must place it behind the existing inventory to maintain the FIFO method.
As customers place orders, the older stock will always be sold first.
Inventory replenishment in the FIFO method example:
- The warehouse receives another 150 units of Product X (Inventory Batch 3) at $16 each on 1st May.
- Inventory Batch 3 will be placed behind Inventory Batch 2.
Advantages and drawbacks of FIFO inventory management
It's important to weigh the pros and cons of the FIFO method. Depending on your business and the industry you are in, there are certain advantages and drawbacks.
Advantages
Reduces waste in your inventory
A major advantage of the FIFO method is its inventory and product waste reduction. The whole point of FIFO is to ensure the oldest inventory gets pushed out first, which helps you be more efficient in your inventory buying.
This is beneficial in industries with perishable goods. FIFO helps reduce the risk of your stock going bad, especially in perishable items or products with an expiration date.
Streamline your inventory management process
The best advantage of implementing the FIFO system is the ability to streamline your entire process from purchasing inventory to fulfillment. Since FIFO means first in, first out, your stock rotation strategy and replenishment are more streamlined.
Maximise your profitability
One advantage of FIFO is maximising profitability. Especially when the cost of goods rises, FIFO leads to a lower cost of goods sold (COGS) because older, less expensive stock is sold first.
This planning improves cash flow and increases net income since the newer (more expensive) stock remains in inventory. Higher net income can improve profitability and provide more cash flow for the business.
Disadvantages
Requires active management
One disadvantage is that FIFO requires active management to ensure that the stock is rotated and that older batches of inventory go out first. If you don't have a robust inventory management system, this can increase operational costs. Not actively managing your stock can lead to inefficiencies or the accidental accumulation of old stock that is harder to sell.
Fluctuating industries
The FIFO method may not be ideal for every industry, especially if you're in an industry with fluctuating pricing environments or markets. This will impact your profit margins and may not reflect the best financially. FIFO works well in industries where pricing environments are stable or rising.
FIFO vs FEFO, which is better?
The FIFO method and FEFO method are widely used inventory management methods, but depending on your industry, one may be better suited to your business. FIFO focuses on inventory that was purchased first and needs to be pushed out. Meanwhile, FEFO focuses on inventory items with immediate expiration dates that must be pushed out first.
FIFO
Some use cases where FIFO is a better method are for businesses with products with short demand cycles. These could be apparel brands, electronics, and CPG.
An example of this could be an apparel brand focusing heavily on seasonality. Retail store managers will push out the inventory they receive first to ensure their first purchased stock gets sold before another inventory order arrives.
FEFO
FEFO stands for First Expired, First Out, and prioritises the first inventory items to expire, which will be the first to go out. This inventory method is used in industries that handle perishable goods, such as food, and businesses with expiring ingredients, such as cosmetics or pharmaceuticals.
FEFO differs from FIFO because, in the FEFO method, expiration dates are first checked and stocked accordingly to ensure there is no dead stock.
Mintsoft’s connected order, warehouse and inventory management software ensures you have features that can automate your inventory management and control how you organise your stock. Mintsoft offers tools like a barcode generator, in-depth stock flow data, and product warehouse allocations. If stock is available across multiple warehouses, you can assign a priority against each warehouse for stock allocation.
Tips for implementing FIFO stock management in your warehouse
The FIFO inventory management system works well if you implement it well across your business operations. Key tips for implementing FIFO include organisation across your inventory, maximising your warehouse space, and having a robust inventory and warehouse management software to implement a streamlined operation.
Tip 1: Organise and label your inventory
The FIFO method only works if you push out your oldest inventory first. Label all your stock inventory clearly. This will help you manage and organise your inventory while helping warehouse staff quickly identify which inventory is the oldest and needs to be used first.
You can use barcode scanning to help warehouse staff easily track products. This also helps send low-stock notifications.
Tip 2: Maximise your warehouse space
FIFO helps ensure you can organise your stock. Maximise your warehouse space and designate separate new and old stock areas. Depending on your warehouse layout, newer inventory should be placed behind or above your oldest inventory. Arrange your shelves so your warehouse staff can easily reach the needed inventory. This will help the stock move forward naturally and more efficiently.
Tip 3: Implement stock audits
For FIFO to work efficiently, ensure your stock levels are where they need to be. You don't want too much stock or too low, but just enough where you can drive fulfillment and never be out of your products.
Implement stock audits that you can check in your inventory management system and, if possible, physically to ensure that FIFO is followed correctly. This will help catch any errors or mistakes early. For the food industry and perishable items, this can be part of the routine to catch stock items almost about to expire.
Tip 4: Use an inventory management software
In order for the FIFO system to be effective, you need inventory management software that is intuitive and expansive. As your business scales and grows, you need a software tool that scales with it and offers expansive features.
Features such as in-depth analytics and reporting on your sales channels and products. Features that benefit your inventory management system include generating barcodes, stock alerts across warehouses, a stock-flow data report, and a way to manage fulfillment.
Tip 5: Train your staff
The final tip for implementing the FIFO management system in your warehouse is to train your staff on the FIFO methods and why FIFO is the system the business is following.
Your warehouse staff should know the movements from receiving the stock to the end fulfillment process, why using the old stock first is necessary, and how to keep the stock rotation system going.
Track product entry and exit dates for FIFO with Mintsoft’s inventory management software
Implementing FIFO effectively gives your business a major advantage that will streamline your inventory management process, reduce inventory and product waste, and maximise your profitability.
Mintsoft is a powerful order fulfillment software with in-depth tools to maximise inventory management across your business locations, warehouses, and 3PL partners. Track product entry and exit dates with Mintsoft and explore key features. Mintsoft scales with you as your business grows to ensure you have maximum visibility when implementing the FIFO system across your business.
Book a demo to explore key inventory management features and ensure your inventory management works effectively.