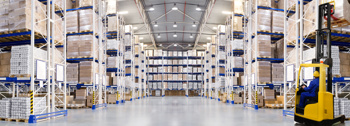
How to improve your order fulfilment process
1. Pick the right order fulfilment strategy for your business
There are various order fulfilment strategies that you could implement to improve your fulfilment process. Choosing the right strategy based on your business size, needs and products being sold can result in processes being clear, simplified and tailor-made for you.
Common order fulfilment strategies include:
In-house fulfilment - Managing and fulfilling orders from your own warehouse(s).
Third-party fulfilment - Outsourcing order fulfilment to a third party, i.e. a 3PL provider, fulfilment house, distributor.
Drop-shipping - Products are sold by you, however orders are produced, fulfilled and shipped by the supplier, directly to the customer.
Depending on your business, one of these strategies, or perhaps a combination of multiple, may provide you the optimal performance you’re looking to achieve.
2. Have accurate inventory tracking and demand forecasting
To improve your order fulfilment processes, you need to be on top of the inventory you have, where it is and how often you need to replenish or stock-up ready for peaks.
Tasks such as regular stock-takes and audits can minimise the chance of you losing inventory, having items in the wrong warehouse locations or experiencing stock-outs. These tasks can help you identify and rectify errors quickly, before they lead to mistakes further in the order fulfilment process.
Having this visibility of your current stock levels is crucial for your day-to-day operations; however, you also need to be prepared for any seasonal peaks. By performing demand forecasting, you can use historic order volume data to predict and plan for the volumes you expect to see in upcoming peaks. Find out more on how to manage peak shipping seasons in our blog.
3. Improving your order processing operations
Every order you receive for fulfilment needs to be processed before it’s sent for picking. If you’re doing this manually, you’re spending a huge amount of time validating addresses, arranging shipping and perhaps even creating batches for picking.
As customers expect quick turnarounds and speedy shipping, manually processing orders can delay orders being despatched.
There are technology solutions that can help speed up and improve your order processing, an order management software can automatically validate order data fields (flagging any that are missing mandatory data), automate courier selection, print shipping labels, and batch orders ready to be picked efficiently.
4. Optimise your picking and packing methods
Picking and packing is a time and cost-intensive warehouse activity, therefore it offers the most potential to be optimised to improve your order fulfilment processes. Similar to the fulfilment strategies, the picking methods you choose will depend on your business needs, size, the amount of storage space you have and the types of products you hold.
Common picking methods include:
Piece picking - the process of picking orders one-by-one.
Batch picking - also known as multi-order picking. The process of picking multiple orders at once.
Zone picking - the process of only picking items in a specific warehouse zone.
Wave picking - sometimes known as cluster picking. The process of picking multiple orders, across different zones simultaneously.
Some of these methods are more complex than others, and therefore to ensure accuracy and coordination across your warehouse, software such as an order management system should be used. For more information on picking and packing best practices, read our full picking and packing guide.
5. Integrate technology into your processes
Order fulfilment is a sequence of warehouse processes that need coordination, control and accuracy, to be successful. Trying to handle all of the moving parts of your warehouse manually can quickly become unmanageable and that is where technology can come in useful.
A good order management software (OMS) can help you to automate processes while reducing errors and increasing speed to despatch. An OMS can improve parts of your order fulfilment process, such as:
- Order import from multiple sales channels
- Order validation
- Inventory sync across sales channels
- Automated picking batch creation
- Barcode-scanning enabled picking
- Despatch document creation & printing
To find out more about how automation can be utilised in warehouses, please read our article on the benefits of warehouse automation.
6. Look to continuously improve your fulfilment process
As customer behaviour is ever-changing, businesses fulfilling their orders also need to adapt to meet demand. By adopting technology, your processes can be easily amended to meet the customers needs.
The technology you use, whether it’s simply software, or more complex systems such as AMRs, can help you to continuously improve processes, increase speed to despatch and achieve better accuracy.
What is order fulfilment?
Order fulfilment is the process of getting products into your customer’s hands. It involves every aspect of your operations from the moment an order is placed, through to despatch; including:
- Order management
- Stock control
- Picking and packing
- Shipping and delivery
- Returns
For a more detailed explanation of order fulfilment, what it involves and it’s common challenges, please read our full guide to order fulfilment.
The importance of the order fulfilment process
The order fulfilment process is a complex sequence of actions that need to be taken, to ensure orders are fulfilled on time and in full. If one part of the sequence incurs an error, or is not completed, the remainder of the process is likely to be affected.
If the order fulfilment process is managed correctly and at optimal speed and efficiency, it can ensure orders are fulfilled and despatched quickly as well as delivering a great customer experience by the customer receiving the correct goods, in a delivery timeframe they expect, minimise the chance of the customer returning the goods and hopefully encourage them to purchase again.
Improve your order fulfilment process with Mintsoft’s Order Management Software
Technology and software can go a long way to improving order fulfilment processes within your business; a good order management software will help with order, inventory and picking operations.
Mintsoft’s order management software can help you increase your fulfilment efficiency, order picking accuracy and speed up the entire fulfilment process with automation capabilities. To find out more about Mintsoft, please take an interactive tour of the platform.
If you’d like to know more before looking at software options, please read our full guide to the order fulfilment process.