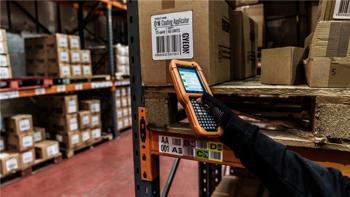
Is it time you ditched paper-based picking?
Here’s what other 3PLs are saying
We know, a software provider telling you ditch paper and replace it with technology… what’s new?!
We’re not going to talk about Mintsoft (much) and instead, highlight the tangible benefits you can expect to see from ditching the paper, based on what our customers have told us about picking with tech.
Better inventory control
The nature of using paper-based picking means that your inventory data is almost instantly out of date. By using your tech, you should have a real-time view of inventory levels, that are accurate and easily maintained because everything being picked is verified via barcodes.
Director of Operations at Airbox Fulfilment, Ben Smalley said:
"One of our warehouses has up to 5000 part locations, and Mintsoft gives us the tools to have a clear view of our inventory across all locations and helps us manage tasks such as picking and replenishment, smoothly and efficiently."
Meet ESG commitments
Ditching the paper means you’re positively contributing to the effort of making your business more eco-friendly. There are so many reasons to do it from a sustainability point of view:
- you’ll save money on paper and waste disposal
- you’re not producing emissions from regular paper deliveries
- you’ve saving energy by not using printers
- you will make your business more desirable to other eco-conscious brands that are looking for a warehouse or 3PL partner.
Cain Fleming, Co-Founder and Operations Director at Green Fulfilment said:
“We were using a paper-based system, so as you can imagine, there was quite a lot of waste and being Green Fulfilment, we were keen to try and cut our paper usage. [When moving to Mintsoft] we moved straight to a scanning based system - we use scanners to pick and also to facilitate transfers within the warehouse.”
Increase picking accuracy and speed
Similar to the inventory control, your picking accuracy and speed will increase due to using barcodes during the picking and packing process. When everything in your warehouse is allocated a unique barcode, and that’s verified via a scan before it’s packed, we’ve been told it’s virtually impossible to get it wrong!
Haul + Store CEO and Co-Founder, Hamilton Butcher said:
“It's never 100% but it's gone from being maybe 70% accurate to 99%, which is an enormous difference. And of course the speed at which we can process all of those orders now is tenfold.”
Futureproof your business
As your business grows, so does your order volume - the expectation to meet demand and continue to deliver the same service level remains the same, even during peak periods.
Tech-based picking processes enable smooth and efficient working, and gives you the confidence to grow your orders, your team and ultimately your revenue without the fear of errors!
Claire Lisle, Head of Information Technology Services at TSP Fulfilment, said:
“In terms of growth, Mintsoft has helped us immeasurably. Before implementing [Mintsoft], we managed fulfilment processes manually, and it was getting to the point of being unmanageable.”
Ditching paper-based picking with Mintsoft
Whatever your motivation for switching from paper-based to tech-enabled picking processes, Mintsoft has the solution. With connected order, warehouse and shipping operations supported by barcode scanning technology and a mobile picking app, the system will improve your picking accuracy and speed up fulfilment. To find out more, book a demo with one of our ecommerce fulfilment experts.