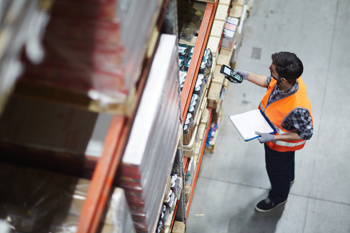
With the recent supply chain problems and warehouse space shortages within the transport and logistics industry, it’s no secret that many e-commerce businesses and third-party logistics (3PL) partners are struggling to fulfil orders at the rate in which they need to.
As the e-commerce sector continues to grow, meeting customer demand and exceeding expectations on fulfilment and shipping time is a priority for both online retailers and logistics partners. However, it’s clear that many businesses are falling short of the number of warehouse operatives needed to efficiently run the fulfilment process, adding further challenges to the industry.
Clare Bottle, CEO at the UK Warehousing Association (UKWA), commented:
“Today’s market is tougher than ever before for the warehousing sector. Labour shortages are no longer limited to the Christmas peak trading period nor are they restricted to warehousing’s famous ‘Golden Triangle’ in the East Midlands.
“In light of the failure of Government to recognise or even mention the role of warehousing and logistics in last month’s Levelling Up white paper, this research is particularly timely, providing an important evidential basis for UKWA’s continued representation to policymakers for
more support in the face of critical labour shortages.
“Indeed, a recent poll of our members confirmed that labour shortages are the number one concern for 2022 and our National Conference next week (March 8-9th), will focus on the theme of Building Tomorrow’s Workforce Today.”
Having analysed data from Indeed for all the vacancies for warehouse operatives, Mintsoft found that London – which has 233 openings – is the UK location with the highest number of vacant warehouse operative jobs and the area with the biggest shortage. With 219 job vacancies, Bristol is second, followed by Birmingham and Northampton.
The locations with the biggest shortage of warehouse operatives were as follows:
Ranking |
Location |
Number of warehouse operative roles |
1 |
London |
233 |
2 |
Bristol |
219 |
3 |
Birmingham |
188 |
4 |
Northampton |
146 |
5 |
Leeds |
129 |
6 |
Nottingham |
125 |
7 |
Milton Keynes |
122 |
8 |
Leicester |
117 |
9 |
Manchester |
101 |
10 |
Coventry |
98 |
11 |
Bedford |
90 |
12 |
Sheffield |
86 |
13 |
Swindon |
80 |
14 |
Peterborough |
77 |
15 |
Doncaster |
77 |
16 |
Stoke-on-Trent |
73 |
17 |
Bradford |
71 |
18 |
Exeter |
70 |
19 |
Warrington |
70 |
20 |
Derby |
69 |
As you can see, this is a nationwide problem and a universal challenge across the majority of regions of the UK and businesses need to be able to adapt to this skill shortage, whether that’s new training initiative, wider opportunities for new staff such as apprenticeships or investing in technology to streamline existing processes.
How can 3PLs, warehouses and retailers adapt and overcome certain industry challenges?
It’s predicted that during 2022, increased shipping costs are here to stay, inventory levels will remain high, staff shortages will continue and warehouse space will be hard to get.
Therefore, if getting hold of more warehouse space or additional workers isn’t an option, utilising existing warehouse space and employees better is pivotal to survival. 3PLs and fulfilment houses, as well as retailers with their own warehouses, should look into implementing technology such as an order management system (OMS) to help with this.
The features offered by a cloud-based OMS will allow e-commerce businesses to be more efficient by using platform data to make more informed and calculated decisions – whether it be around inventory, returns processes or even selecting the best courier for the job.
Automating time-consuming tasks will not only save time but help to reduce errors during tasks that are ripe for human error, meaning warehouse workers will be able to work smarter, not harder - freeing up time to allow for instances where there are potential staff shortages.
Efficiency is key within a warehouse or fulfilment house to ensure orders are picked, packed and shipped as quickly and as accurately as possible, making it even more important to have a system in place that streamlines the picking and despatch operation. Having an insightful overview of inventory – such as best sellers and less popular items makes it easier to decide what, and how much of certain stock you need, removing the risk of wasting warehouse space.
Rob Hodgson, WMS and E-commerce Fulfilment Expert at Mintsoft commented:
“With additional challenges being caused as a result of the current supply chain issues, many online retailers are looking to outsource their logistics and partner with a 3PL that can offer streamlined fulfilment and shipping solutions as they look to keep ahead of growing demand.
“Expectations of logistics partners such as 3PLs and warehouses are ever-increasing, and working efficiently has never been more important. To best serve clients and their customers, orders must be completed efficiently – this means speed and accuracy are pivotal.
“The global warehouse management software market size is expected to grow from USD 2.8 billion in 2021 to USD 6.1 billion by 2026, at a CAGR of 16.7% which is being driven by the boom in e-commerce.
“The data shown as part of this campaign confirms that many fulfilment businesses are struggling to recruit the staff they need with the skills needed - industry-specific recruitment specialists have even commented that they've never been busier when it comes to fulfiling roles in the warehouse and logistics sector.
“It's time to enhance processes in order to improve existing warehouse efficiency and space optimisation by empowering current staff with the right conditions and technology to make it easier for them to succeed.”
Five Reasons to Invest in a Warehouse Management System (WMS)
Online shoppers now choose convenience over brand loyalty, meaning how orders are picked and packaged, delivery costs and timings, and ease of returns are pivotal to offering a good service to customers. Something as small as a payment error, missed order or delivery issue can be enough to lose customer loyalty these days.
Investing in technology such as an order management system and being able to automate time-consuming tasks and processes, means that warehouse staff can work more efficiently and make better use of existing warehouse space. In addition to streamlining fulfilment operations, implementing an inventory management system has many other key features and benefits:
-
Keep inventory costs low
E-commerce and multichannel inventory management software gives users the ability to automatically monitor stock levels and sales data for each item, helping to improve the efficiency of adding new items to inventory, tracking sales, and updating stock levels.
The ability to gain automated insights into product information is also a key benefit, allowing you to know the best place to store inventory, and how to handle certain items of stock (fragile, flammable etc.).
-
Avoid stock-outs
Keeping on top of inventory management can be a challenging task, especially during peak seasons. Stock-outs can lead to unhappy customers, stressed employees, as well as a dent in profits.
An order management system with API integration capabilities will automatically take control of stock levels by connecting with other systems and channels such as marketplaces and online stores, meaning the risk of overselling items is removed. Never again will you have to inform a customer that the product they’ve just spent time ordering, isn’t actually available.
-
Connect with all systems from a centralised platform
As well as helping to reduce to risk of stock-outs, API integrations also help to trim down complicated processes and automate time-consuming tasks and entire workflows, helping to save time and remove the risk of human error. By opting to invest in order and warehouse management technology with integration capabilities, the need to log into multiple platforms is removed and users are provided more secure and faster data transfer – putting both your and your customer’s mind at ease.
-
Make data-driven decisions
Using a cloud-based order management system will support delivering a more responsive and consistent service by automating unavoidable admin tasks.
By providing complete visibility over your business information from one centralised platform, knowing where and what you are selling is made easier, drastically reducing errors and helping to make informed, data-driven decisions by providing deeper insights for forecasting and demand planning.
-
Hassle-free invoicing for clients
Billing clients for various costs is one of the most time-consuming aspects for fulfilment and logistics partners. An order management system is able to provide clear and transparent client invoicing when it comes to charging for fulfilment costs, and most of them are able to further break down into associated areas within this; from shipping costs to pick, pack and storage charging models.
Methodology
We analysed data from Indeed under the search term 'warehouse operative’. We then broke this data down by the regions of the UK they were being advertised in. From this, we found London had the highest number of job vacancies in this particular field - and ultimately the biggest shortage of warehouse operatives.
This is based on data collected on Monday 21 February 2022.