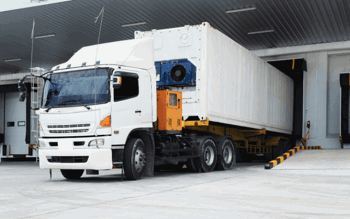
The warehouse receiving process is one of the most important phases in supply chain management. Any error during this process can have knock-on effects that cause significant issues for the subsequent warehouse operations.
A poor receiving process can lead to problems that impact customer experience, with cancelled orders or lengthy fulfilment times will harm profitability and reputation if left unresolved.
In this article, we outline the various steps and best practices necessary to achieve an efficient warehouse receiving process, as well as how Mintsoft's warehouse management software can support and help you optimise your order fulfilment operation with ease.
What is the warehouse receiving process?
Warehouse receiving is the process of replenishing stocked inventory in the warehouse. It is the first step in the process of delivering an order to a customer.
The process includes delivering, unloading and storing ecommerce inventory in a warehouse or fulfilment centre.
A well-established warehouse receiving process can help make inventory management and fulfillment run smoother, cheaper and more efficiently.
What are the steps in the warehouse receiving procedure?
The warehouse receiving process is not as simple as just purchasing goods from the suppliers and having them arrive at your warehouse in a few weeks. In order for this part of the supply chain to fit into the wider process seamlessly, you must take a strategic approach.
We have outlined the steps that should be followed in any strategically sound receiving process below:
Proper documentation
Before you can even think about ordering or receiving the goods, you should always ensure you complete pre-receiving tasks to ensure your cargo is delivered correctly and on time.
The main element of pre-receiving is proper documentation that should be sent to suppliers and shipment partners that states your packaging requirements. These requirements will include:
- Label information
- Number of items per container
- Number of packages per pallet
- Number of items per carton
- The required size and weight
In most cases, the process involves answering what’s known as a Warehouse Receiving Order label (WRO), which will be attached to each stock. The label contains a barcode that can be scanned and integrated with warehouse management software to view data on your purchase and check you are receiving the right order.
Receiving and unloading
The following step in the warehouse receiving procedure is to receive and unload your shipment. When the delivery vehicle arrives at the unloading area, warehouse staff should be prepared to meet the shipment provider to receive the cargo.
Ideally, unloading bays should be packed back-to-front in the reverse order of the delivery schedule so that warehouse operatives can unload inventory immediately without having to first move other cargo.
Depending on the size and volume of the order being received, heavy lifting equipment such as forklifts and pallet jacks may be required.
Staff should be well trained in the handling and receiving process to avoid accepting incorrect shipments. Where there are any issues, concerns or discrepancies, the receiving teams should discuss them with the shipment provider before signing off the delivery notice.
Inventory count
Once the stock has been received, the cargo should be unloaded and counted to ensure that the correct quantity was shipped. Any errors or inaccuracies should be communicated to the shipping provider as soon as they are spotted.
Inventory inspection
As well as counting inventory, it should also be inspected for possible damage caused during the shipping process. Damaged products should be set aside and returned for replacements. Other elements that should be inspected include the product codes, the integrity of the seals and the list of products on the WRO compared to the products delivered.
Inventory storage
The final phase of warehouse receiving is the inventory storage process which involves arranging and storing the new products in the warehouse. The products can be stored on shelves, pallets, or in bins.
Mistakes many businesses make with warehouse receiving
The main goal of any business that receives stock should be to unload, check and store inventory as efficiently and accurately as possible, as well as make sure all inventory is accounted for.
When warehouses or businesses don’t have a set of procedures or a robust checklist in place for unloading and receiving goods, there is a risk of ending up with inaccurate or lost inventory, leading to incorrect inventory counts that could end up impacting consumers ordering stock that in reality does not exist.
To avoid this, businesses should provide warehouse staff with resources that outline a clear and streamlined process, including a step-by-step task list to follow when receiving, as well as a list of questions to ask and details to check.
Warehouse receiving best practices
There are several ways businesses can enhance their warehouse receiving process. We have collected some of the best practices you can implement, whether you manage your own warehouse operations or work with a fulfilment partner such as Mintsoft.
Introduce a warehouse management system
Warehouse management systems (WMS) are the go-to solution for ecommerce businesses, 3PLs or fulfilment partners that manage the warehouse process, from receiving, to packing and shipping out to consumers.
With a WMS, warehouse operators have access to real-time data and can scan items in quickly, seeing inventory numbers change immediately after the warehouse receiving process. This system can be integrated with other fulfilment solutions such as inventory management software that can track and manage inventory, even configured to automatically reorder stock, making sure that you never run low.
Track inventory metrics
A robust warehouse receiving process will make tracking inventory and attributing logistics costs much easier. This is especially helpful if you store inventory across multiple warehouses or fulfilment centres. With the right warehouse technology, you can monitor and manage all inventory from one central dashboard.
Run inspections
If stock comes in damaged, missing, or incorrect, you want to make sure it is returned before it is too late. Checking stock as it is received is recommended, but may not always be possible to do in its entirety or issues may be initially missed. We recommend undertaking periodic inventory audits such as physical counts and cutoff analyses also catch inventory imbalances before they become a problem and may influence your next round of warehouse receiving.
Double check documentation
Paper work is the least glamorous part of warehouse receiving, but double checking your documents and making sure that receiving inventory matches your purchase order will save you time and money.
Implementing a system for all receiving and shipping documents where each type of document has a numbering system and different forms are labelled in sequential order makes it easier for staff to check paperwork thoroughly and identify missing inventory.
Benefits of optimising the receiving process
Having a steadfast warehouse receiving process that adheres to best practices is an investment that will set your fulfilment operation up for success. As it is the start of the process, a structured warehouse receiving procedure will help make sure that the right items and the right quantity of items are available and ready to be fulfilled.
Here are just a few of the benefits you can expect from optimising the warehouse receiving process:
Increased stock count accuracy
Accurate stock counts are vital to businesses managing their inventory. Avoid stock shortages, forecast demand, reduce inventory shrinkage rates and maintain healthy net profit margins.
A comprehensive receiving process checklist for staff or automation through inventory scanning for real time updates help to ensure the contents of a delivery match the original order.
Fewer stock shortages and dead stock
Stock shortages can cause customers to seek products elsewhere and lead to negative reviews that harm your brand’s reputation. Alternatively, overstocking (known as dead stock) leaves businesses with a surplus of inventory that cannot be used to deliver a return on investment, let alone a profit.
An optimised warehouse receiving process will work towards preventing both of these issues such as a supplier delivering the incorrect quantity ordered.
Efficient inventory storage
Another benefit of improving your warehouse receiving process is that it can help with inventory storage strategy, making sure inventory is stored in the most efficient, cost-effective way possible.
Upgrading your operations using a WMS (warehouse management software) to scan inventory when it is received will allow staff to retrieve instructions on how to unpack and store inventory, as well as how to pick, pack and ship items once sold.
How Mintsoft can help you improve your warehouse receiving procedure
If you are a B2B, B2C, wholesaler or ecommerce store and you are fulfilling orders from a warehouse, you should ensure your warehouse receiving is a slick and error-free process that compliments the rest of your fulfilment operations.
Investing in warehouse management software will make sure you can count, check and organise stock faster and more accurately, providing you with real-time data and insights directly from the warehouse floor the moment you replenish your stock.
Mintsoft’s warehouse management software allows you to track inventory levels, increase picking and packing speed and accuracy, as well as monitor shipments. It also lets you create reports that inform you of further ways to improve, saving you time and money.
Book a demo to find out more about how Mintsoft can support your business today.