Guide to Warehouse Management Systems (WMS)
If you’re looking to learn more about warehouse management systems (WMS) and how you can manage and automate warehouse processes, inventory and orders all in one place, this in-depth guide is for you.
An introduction to warehouse management systems
In this article, we’ll cover everything you need to know about WMS systems, including:
If you’re looking for different information on warehouse management systems, browse the range of blogs and customer stories we have on WMS, or explore our warehouse management software page to learn how we can help your business.
What is a Warehouse Management System?
A Warehouse Management System (WMS) is an application that helps warehouse operators and 3PLs control and track inventory levels, orders, and deliveries in a warehouse. By automating many of the tasks associated with managing a warehouse, such as tracking inventory levels, calculating the most efficient storage layouts, and generating pick lists, a warehouse management system can help businesses improve their overall efficiency and productivity.
A WMS can be used for both small and large warehouses but comes into its own with floors of over 20,000 square feet and the demands placed upon start to get complex. At this level and above it is sometimes referred to as an ERP system or enterprise resource planning.
Warehouse management systems have taken off in significance of late. Not only has online shopping increased along with mobile phone and internet usage, but the pandemic accelerated the need for efficient and automated solutions for companies that sell online.
With ecommerce growth resulting in a predicted €24.8 billion increase (10.41% CAGR) in the global warehouse automation market by 2026, along with the complexities of multi-channel listing and courier management, the new breed of warehouse management systems are practically now a necessity for warehouses, 3PLs and ecommerce retailers to compete.
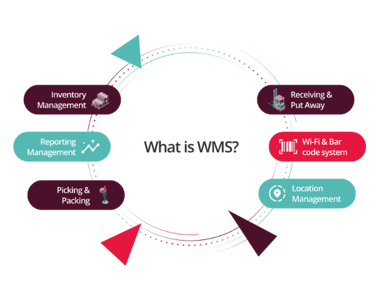
Where does a warehouse management system fit into the supply chain?
A critical part of the supply chain, warehouse management is responsible for the storage and movement of materials that are essential to the operation of businesses. It includes the receiving, storing, and shipping of goods, as well as the management of inventory levels and stock locations.
Therefore, the supply chain can only operate as quickly, accurately and efficiently as warehouse processes permit. Without effective warehouse management, the flow of materials would be disrupted, and businesses would be unable to function.
A WMS is often used alongside or even integrated with other related systems such as an ERP (enterprise resource planning), order management systems, or a TMS (transport management system) such as shipping management software.
Warehouse management systems play a critical role in warehouse and distribution centre operations, such as picking goods from shelves for shipment or putting received goods away. They work by tracking incoming data from barcode readers and RFID tags to ensure that inventory management in the ERP system has the latest information. It ensures a link is integrated between the ERP system and the WMS to synchronise this inventory data.
The ERP system can handle anything from accounting, and invoicing, to order and inventory management, while the transport management system is where the shipping process is managed. It is a repository of detailed shipping carrier information as well as a communication system for planning, executing, and tracking shipments. In some cases, the TMS is integrated with the WMS to improve coordination across inbound and outbound logistics tasks.
Orders are typically imported automatically from ERP or order management systems that are integrated with the TMS. This will include customer data such as name and address, as well as item details for ensuring the correct products are shipped. The TMS will then output shipment details (such as tracking information, the carrier name and cost) that are needed for the ERP system to carry out its accounting and order management functions. These details may also be sent to the Customer Relationship Management (CRM) module to update customers on the status of their orders.
The 4 types of Warehouse Management Systems
In order to choose your warehouse management system, it’s critical to understand the different types of WMS that are available. There are four types of warehouse management systems, including:
- Standalone system
- Cloud-based system
- Integrated with ERP
- Supply chain modules
Let’s take a look into what each different type of WMS system does and how they operate.
Standalone WMS vs Integrated WMS
Now you have a better understanding of various types of warehouse management systems, it is time to start thinking about which type of WMS will be the best fit for your business.
When it comes to warehouse management software, you have two main options.
You can either choose a standalone system that can be integrated with the rest of your operational systems or choose an already integrated solution where the WMS is part of the same software system that includes order management, inventory and accounting.
Standalone WMS
A standalone WMS is a specialised warehouse management system designed to maximise warehouse efficiency. It can be seamlessly integrated with other systems such as inventory management software, order management software, and shipping management software, however, its primary focus is on warehouse management features.
There are a few benefits of having a standalone system, from having access to a number of advanced warehouse management features such as warehouse picking options, cycle counting, cross-docking and advanced reporting features, to integration capabilities with other systems such as accounting software, order and inventory management software, purchase order systems and other solutions such as ERP and TMS.
There are some potential disadvantages to standalone systems to be aware of. Given the separation between the various systems, your staff will need to log into multiple different platforms in order to complete some functions. There is also the possibility of real-time integration issues where the WMS data is updated at a different rate to other systems your business uses, running the risk of the warehouse team having data that can be anything up to a day behind the rest of the company.
There is also the factor of cost. By investing in, implementing and maintaining multiple systems to sustain the core functionality of your business needs, costs will quickly accumulate. It is therefore important to calculate the ROI a standalone system will offer and offset that against the increased tech spend.
Integrated WMS
An integrated warehouse management system can take many forms, but it is essentially a solution either included in your existing ERP of back office software or an additional module that is sold by your ERP provider. This means that it will share the same database as all of your orders, inventory, accounting, CRM and reporting.
Centralised data is a big benefit of integrated WMS systems as you can gain real-time accuracy and consistency across your data as well as make sure all staff have the same up-to-date information. Workflows are simplified through integration, leading to simplification and seamlessness throughout the order cycle. Finally, your overall technology spend is likely to be lower compared to purchasing and implementing multiple systems.
A potential drawback of integrated systems is the reduced functionality options, which may mean your business lacks some of the more complex and advanced functionality of a standalone solution.
As with purchasing any new software, but especially warehouse management systems, it is important to explore pricing arrangements and all of the other costs you may incur, such as:
- Infrastructure
- Hardware
- Software
- Licensing fees
- Implementation
- Maintenance
- Customization & optimization
- IT labour costs
- Other labour management costs
WMS providers offering cloud-based and integrable WMS solutions such as Mintsoft will handle a lot of these costs themselves, meaning that you will likely only need to consider software, licensing and implementation costs.
Who are WMS Systems For?
It is important to note that warehouse inventory management systems are not just for warehouses. With a WMS system, any company can manage its inventory and distribution processes more effectively - not just 3PL warehouse managers. For example, retailers and wholesalers alike can use warehouse management software to better manage their stock levels, track inventory movements, and generate reports on product performance.
You could be a B2B warehouse operator with multiple warehouses, or you could be a B2C ecommerce brand with listings on multiple marketplaces such as eBay, Amazon, and Etsy. Either way, a warehouse inventory management system can help you speed up your business processes as well as reduce errors and management time spent with effective warehouse optimization.
What are the benefits of a warehouse management system?
A WMS system has many benefits, including improved inventory accuracy, improved customer service levels, reduced inventory costs, increased supply chain management visibility, reduced labour, and admin costs, increased speed of service, sales forecasting insight, and more. As a warehouse manager (or a brand that needs to employ one) this will be music to your ears! Especially if you are often away, or working from the head office. Let's look at each of these benefits in more detail below:
1. Improved inventory system picking accuracy
An effective warehouse inventory management software is a crucial part of business success. Inaccurate inventory buying and picking can lead to low customer satisfaction, high product returns, and ultimately loss of revenue for the company which could be avoided with proper inventory control procedures in place.
2. Improved customer service
Customer service is key to building customer loyalty. With the help of a WMS system tied to a user's record, customers are seeing companies create more personalised customer service experiences based on their needs and preferences. This leads to customers feeling appreciated and valued, which could lead to increased customer loyalty. With fewer errors and a faster, more streamlined process that touches fewer people from order to delivery, customer satisfaction only improves.
3. Reduced stock inventory costs
With UK warehouse inventory management costs running in the billions, retailers are doing anything they can to cut down on their stocks. Some of the most effective ways of reducing inventory costs are setting up accurate forecasts, monitoring customer behaviour, and ordering products only when necessary. Inventory costs are generally made up of:
- Capital Costs: - (The opportunity cost of money that could be better deployed elsewhere if it were not tied up in the form of inventory)
- Inventory Costs: - Insuring the stock; Staff costs including clerical management and handling of the stock
- Storage Costs: - The cost of the warehouse or shelf space (especially during peak times)
- Risk Premium: - Spoilage, Obsolescence, Damage, Lost items
- Increased supply chain visibility: The ability of products to be tracked from raw material to the final destination.
With real-time data that is fully integrated with other systems such as a Customer Relationship Management (CRM) program, insight can be gathered to inform the user of trends, problems, and opportunities. For example, seeing long delays from one manufacturer, or increased seasonal demand from one group of customers. Knowing this and acting accordingly helps ensure you can meet - and oftentimes exceed - customer demands.
4. Reduce Time Spent Managing
Labour management is a time-consuming task for companies to manage manually. A reliable WMS system can reduce this time consumption and help scale a business. As orders come in, the system can automatically allocate them - no manual approval at every stage is required.
Warehouse automation can be further increased by batching orders together for order pickers to save the amount of time it takes them to pick and pack the goods. By using barcodes for tracking a package in transit, regular updates can be provided to customers to set their expectations and avoid unnecessary customer service complaints handling -a real-time saver at every stage.
5. Increase Speed of Orders
Next-day delivery is now the benchmark, and warehouse giants such as Amazon and Argos already offer same-day delivery on numerous items. As the competition (and customer expectations) increase, technology such as mobile barcode scanners can be used to increase the speed at which orders can be transmitted from the buyer, through the system, and straight to the picker/packer. With automated shipping label creation too, each stage of the order fulfilment can take place with the least amount of touchpoints and bottlenecks.
Benefits of a Cloud-based Warehouse Management System
As well as choosing between a standalone and integrated WMS, businesses need to decide whether to implement an on-premises or cloud-based WMS.
In recent years, we’ve seen a notable shift towards cloud technology in the warehouse industry, implementing what has been widely described as the ‘paperless warehouse’.
Let’s run through 6 key benefits of cloud-based WMS systems, starting with cloud-based connectivity.
Cloud-based connectivity
Cloud-based software has been designed specifically to work in unison with other systems. By working in the cloud, your data such as inventory and financial reports will be updated with every shipment, incoming delivery, inventory adjustment or warehouse transfer. It also enables greater connectivity options with external systems such as those of suppliers or distributors.
Data-driven decision-making
Cloud-based connectivity matched with real-time updates allows you to make dynamic, informed, data-driven business decisions.
With cloud-based WMS systems, businesses can quickly identify and resolve issues with high-value goods, as well as generate instant productivity reports on warehouse and staff performance.
With access to real-time data, improvements can be made quickly where needed to generate efficiencies.
Cost-effectiveness
With massively reduced costs for infrastructure, hardware, software and licensing, cloud-based systems offer a much lower total cost of implementation and ownership, eliminating the need for large capital expenditure for on-premise solutions.
Cost savings can be redirected towards growth and scalability, shifting the focus from behind the scenes, to the front of house.
Quick to implement
Because configuration, hosting, setup and implementation are all managed by the cloud-based WMS provider, getting everything set up takes a matter of weeks as opposed to the months or even years a traditional, on-premise solution can take to fully implement.
Continuous improvement
As a cloud-based WMS user, you will receive regular and routine updates as part of continuous improvement, avoiding the disruptive experience of on-premise large version upgrades. This ensures your business is always benefitting from the latest features with no requirement for developers to help update your system.
Integration capabilities
With a cloud-based WMS solution, it’s easy to ensure your entire business operations and systems are integrated seamlessly. For example, for inventory updates, both your accounting and warehouse records will need to be updated and through cloud-based solutions, this can be done simultaneously with data updated instantly.
How to choose the best WMS for efficiency
As you can see from the above, there are many types of warehouse management systems with various advantages and disadvantages, and it really does depend on your business size and requirements as to which one you choose. It’s certainly worth thinking about the flexibility you need, the efficiency you require and the growth your business plans to see in the next five years.
Consider price
Although monthly costs for cloud-based warehouse systems are reasonable, if you add them up over the course of 5 or 10 years, there will be a premium that is paid for the cloud service rather than the on-site one. Consider WMS system pricing similar to car or van leasing - if you need a reliable, fully maintained transport service then the monthly costs are justified but there is no denying that over the course of many years, it would be cheaper to pay upfront for a vehicle you owned. It’s the same for choosing your warehousing management system.
Learn more about how much warehouse management software costs
Consider connectivity and support
With a cloud-based system, you are reliant on your internet connection and without it, many SaaS warehouse management systems will not work whatsoever unless they have an offline mode, which doesn’t always allow full functionality. In the same way, you are also reliant on them as a vendor to manage speed, security, compatibility, and all IT-related issues. You will not be able to make changes to the code or even view it to understand it, and will instead need to submit a support ticket or feature request, and trust that the provider will get around to your issue quickly and solve it satisfactorily.
Mintsoft, for example, is at the cutting edge of warehouse management and as such offers a fully managed and integrated cloud-based warehouse inventory management software This means a customer is free to upgrade and downgrade their package as their business needs change. As a managed service it means you don’t need to employ a technical team to manage IT or software errors - we take care of it all behind the scenes.
Consider a standalone WMS system vs ERP
If you have existing warehouse management software tools that handle all your needs and are well embedded into your processes, a standalone warehouse management system may be more suitable for you. Typically standalone warehouse management solutions are more focused in their features and tools, and so can offer very niche features which may be useful to you if your distribution is already at an advanced level. Usually, they can integrate with other systems, but sometimes there could be discrepancies. Separate logins and processes sometimes prompt users to make their own shortcuts which can be insecure or separate from other users, and may cause confusion, data blind spots, or errors.
If you are looking to upgrade multiple parts of your order management system at the same time, an integrated ERP module approach straight out of the gate would make the most sense for larger operations. With a centralised point of record and global database, integrations with accounting systems, listings, and courier services can be more readily relied on. When trying to find data, it should now all be accessible and understandable, with blind spots reduced and mistakes easier to pinpoint. With this ease and reliability come the added benefits of insight and reduced costs.
Cloud-based WMS or supply chain module
As with most online services nowadays, you don’t need to download the software to use it - the server has all the data and the client just accesses it. The same principle applies to cloud-based warehouse management. The server can be very powerful and the user can access it with a relatively low-powered, simple device - all the hard work is done in the cloud. This means high IT infrastructure costs can be a thing of the past.
Although a cloud-based WMS such as Mintsoft offers almost unlimited scalability and flexibility, a supply chain module may be the better option if you’re a large, growing business that operates across an entire supply chain.
If you'd like additional help with choosing the best WMS for you, read our article on how to choose the best warehouse management system.
Warehouse management system features and processes
Managing a warehouse requires a lot of time-consuming tasks, such as hiring staff, training, insurance, rotas, HR policy, layout and so on. You might well already have warehouse management solutions in place to help with those tasks, however, a WMS system focuses on helping with the core function of the warehouse: incoming inventory, picking, packing, and shipping.
Incoming Inventory
The importance of warehouse stock control systems cannot be overstated. Many WMS systems are aware of your current stock levels and when they reach a certain level, an order for replenishment can automatically be sent to your supplier. As the new stock arrives it is scanned with a barcode scanner. This barcode scanning data is sent to the WMS to adjust stock levels (inventory count) accordingly.
More advanced applications of warehouse management software will know where in the warehouse the stock is held and will be able to advise on warehouse layout by suggesting the best place to store certain items. Your warehousing operation will also be able to improve its order processing by the WMS system prioritising the best way to batch orders, which will save time for the staff members doing the item picking.
Picking
A picker is a term given to a warehouse operative that gets the orders from the shelves and moves them to the packing area. Armed with a mobile app, the WMS system will prioritise orders and tell them what items to pick.
In Mintsoft’s case, the app is available as an Android App and easily installed on most current Android devices. You then mount the phone into a handheld barcode scanner which talks to the phone via Bluetooth wireless radio. As the picker scans the item in question, the warehouse inventory management software will check if it’s the right one. If it’s not, then the picker will be alerted and a potential mistake will be avoided.
Picking sounds simple but if you are part of a busy warehouse operation you will be familiar with the challenges that come with multiple shipping methods, order priorities, and the seemingly impossible task of managing the workflow in the most efficient way possible. Given enough data to work with, a WMS system will simplify and improve your workflow to increase warehouse efficiency, reduce time wasted and reduce time spent overall. This can translate to faster order picking, more rest time for staff on the warehouse team and increased productivity.
Packing
The next stop for the product is at the packing desk. To improve efficiency at this station, some warehouses make use of special packaging materials and packaging machines. Where Mintsoft and other warehouse management solutions contribute here is by automatically creating the correct labels and notes for the inside and outside of the package.
Outside of the package the delivery address and the barcode(s) for the appropriate courier(s) will be affixed along with any other labelling, such as a battery warning label or a fragile contents label. Inside the package, it is becoming more commonplace to include a flyer with a discount code, review incentive, or thank you note. These can be personalised and printed by the warehouse management system depending on the time of year, the number of purchases, items that particular customers may be interested in, and so on. As wrong product packaging and delivery leads to 17% of inventory mistakes and, consequently, lost customers, accuracy is essential at this stage - which is why WMS systems are so beneficial to the packing process.
Shipping
When utilising a warehousing management system for shipping, the ideal courier will have been auto-selected and the labels printed. Now attached to the correct package, the item will be moved to an edge of the warehouse on an outgoing collection palette, ready for the courier to pick up. Scanned again, the software knows the package has left the building and is with the courier. At every scan stage, the WMS system can be set to update the customer as to the progress of the order and the expected delivery date and time. Giving them full visibility of their parcel, and in turn, giving them more confidence in your business.
Customers don’t want to be bombarded with information but just kept up to date, so it is usual to set the automations to fire when:
- The purchase order is received,
- It's dispatched from the warehouse,
- And when it’s with the local courier
The customer never needs to know the complicated choices the warehouse system has made routing the package through the fastest courier available for the price, given size, weight, timeliness, border considerations, and availability. As a retailer, warehouse, or 3PL manager, it’s not something you need to worry about anymore either. Instead, you can have the confidence that your WMS system is handling your shipping.
Reporting
Warehouse inventory management systems also allow you an understanding of the warehouse processes that are in play through data-led reporting, allowing you to improve your warehouse optimization. All the data points in your warehouse system are readily available and can be put together in ways that illuminate opportunities and threats. For example, with monthly predefined reports, you can quickly see which products are in most demand, and which couriers are working well or are not performing up to their Service Level Agreements (SLAs). You can also see gross profit, as well as profit per SKU reports, which can help establish where marketing budgets could be allocated or extra resources invested. Tracking errors can be highlighted and business processes improved.
Warehouse management best practices
The bulk of this warehouse management guide so far has covered the ins and outs of warehouse management and WMS, but there is more to success than simply having a sophisticated warehouse management system. To make sure your warehouse is as efficient and optimised as possible to satisfy your customer demands for speed and flexibility, there are a number of warehouse management practices to adopt.
How to gain efficiency in the warehouse
One of the best ways to reduce costs and processing time is through automation. Eliminating the need for a human to check orders, marking them as allocated, fulfilled and ready for dispatch speeds up the order processing leading to cost savings and improved customer satisfaction.
By using the automation that software such as a warehouse management system offers to speed up order processing, warehouse operators can focus on other tasks such as picking, packing and shipping orders more quickly.
The use of mobile barcode scanning is a great way of reducing the possibility of human errors from incorrect data inputs, as well as reducing costs and processing times.
By integrating your warehouse management system with your inventory system, your team will be able to easily scan goods in and out of the warehouse, updating inventory levels, prioritise packing lists, use a range of order picking techniques and perform instantaneous inventory counts using a barcode scanner.
You should also regularly review your practices to measure efficiency through reports. It is critical to monitor your warehouse’s stocking, pulling and inventory management processes by analysing the following metrics and reports on a regular basis and make decisions based on your findings:
- Variance reports
- Processing cost per order KPI
- Time to ship KPI
- Reasons for return
- Supplier reports and history by supplier
- Empty bin report
- Expense controls
Multi-Location Warehouse Management Best Practices
When operating out of multiple warehouses and store locations, it’s important to keep in mind best practices when managing a successful multi-location warehouse strategy. To make sure scale does not impact efficiency, it is important to consider and implement the following best practices:
1. Separate product counts per warehouse
Make sure your inventory management systems are displaying overall inventory levels as well as more detailed information on what is stored in each warehouse. This will prevent overstocking or running out of stock in one location.
2. Establish individual strategies for where to send products
Automate warehouse routing for regions which you are particularly present in, and store slow-moving inventory together conveniently and economically. Popular products should be stocked across all warehouses so orders can be fulfilled quickly.
3. Decide if you will use standard or concurrent warehousing
Standard warehousing means each product has a set location where it should be stored, while concurrent warehousing means inventory can be shared amongst multiple warehouses. Make sure your technology is flexible enough to accommodate both.
4. Divide inventory risk across warehouses
By operating out of multiple warehouses, you can divide your most popular or valuable items so risks are mitigated if something goes wrong.
5. Use inventory forecasting best practices
The added complexity of multiple warehouses means it’s important to be aware of the danger of overselling inventory in certain warehouses.
6. Familiarise yourself with inventory transfers
Have a documented process for employees to follow when needing to transfer goods between warehouses, from sending out from the original warehouse to receiving it in the new one.
Using technology to streamline your pick, pack, and ship process
Warehouses can greatly benefit from the proper utilisation of technology. Investing in warehouse management software can provide a variety of advantages, such as allowing pickers to print documents and labels with ease, creating picking batches tailored to your specific needs, and enabling barcode scanning to eliminate wrong item selections. With the right system in place, warehouses have the potential to streamline operations and gain a competitive edge.
In summary
The main goal of warehouse management is to make sure the right product is at the right place at the right time, with the least amount of friction. Usually, this means the goods going to the customer, as opposed to the management of inputs which would be more of a supply chain solution.
A warehouse management system is an essential tool for modern businesses with a high throughput of inventory. Warehouse inventory systems allow you to track inventory levels, increase pick and pack speed and accuracy, as well as monitor shipments. It also lets you create reports that inform you of further ways to improve. You stand to save an inordinate amount of time and money by automating many tasks.
Book a demonstration with us today to see with your own eyes exactly how the Mintsoft warehouse management system can transform your warehouse or online retail business. We sincerely look forward to speaking with you.
A warehouse management system to help you to pick, pack and ship your way to success.
WMS System Frequently Asked Questions
How does a warehouse management system work?
A warehouse management system works by giving a warehousing business management and visibility of their inventory, so goods can be tracked from manufacturer, to shelf, to customer. This is done through a provider implementing specialist WMS computer software that provides mobile scanners, label printers, and shipping management. A WMS is successful by increasing efficiency, reducing costs and improving customer satisfaction levels.
What are the types of warehouse management systems?
There are 4 distinct types of warehouse management system, including: a standalone system, a cloud-based system, an ERP integrated module, or within a supply chain module.
What is a cloud-based WMS?
A cloud-based warehouse management system is delivered through a SaaS (software-as-a-service) warehouse management software provider. The software is accessible through the internet on any device, where all the information is held on an external secure server.
SaaS warehouse management systems, such as Mintsoft, will often require a monthly fee, which covers the installation and maintenance of the server, alongside upgrades and support.
What do I need to look for in a warehouse management system?
Choosing your own WMS system needs to be thoughtfully researched and planned so it can most benefit you. There are however some key features you need to look for in a WMS system, including: maximum functionality, ease of use, flexibility, reporting features, value for ROI and integrations.
Why are WMS needed?
In the modern day, warehousing businesses around the world need to operate perfectly to achieve maximum productivity to both retain customers and put themselves above the competition. A warehouse management system such as Mintsoft offers an all-in-one solution for recording inventory, order management, shipping processes and much more. Whether a large or small e-commerce business, a WMS system is certainly a good investment.
When might a business need to consider a WMS system?
If your day-to-day warehouse operations are giving you endless problems and loss of revenue, it’s time to consider a warehouse management system. Many issues can arise within a warehousing business, including misplacement of inventory, customer complaints, and the overworking of staff. If these are commonplace in your business and you’re lacking in efficiency, you should certainly consider investing in a WMS system. Your size and the complexity of your operations should factor into your choice, however, it is certainly worth it in the long run.