Warehouse Stock Control: Methods, Systems and Best Practices
Learn about warehouse stock control, why it's important and best practices to follow to help better manage inventory and reduce unnecessary costs.
Introduction to warehouse stock control
Warehouse stock control is essential for any 3PL or retailer as it ensures efficient and effective storage, and the keeping and retrieval of products and inventory.
Many organisations opt to manage their operations with the help of advanced warehouse stock control systems. These systems are made up of computerised software used to track and organise inventory, manage costs and ensure that products are available when needed.
This deep-dive into warehouse stock control systems looks at why they are so important in a warehouse environment, the benefits they provide to businesses, and the potential pitfalls associated with poor stock management.
In this guide, we’ll cover:
- What is warehouse stock control?
- Why is stock control important in warehouse management?
- Pitfalls of not accurately monitoring stock
- Different stock control methods
- Improve warehouse stock control with best practices
- Improve your stock control with warehouse management software
- Frequently asked questions

What is warehouse stock control?
Warehouse stock control is a system used to track and manage the stock availability and movement of goods within a warehouse. It ensures the accuracy and availability of stock by tracking the supply of inbound goods, recording the outbound dispatch of goods, and tracking stock levels across the warehouse.
Warehouse stock control is an essential part of warehouse management that helps meet customer demand, reduce costs and increase efficiency. It is also used to anticipate customer demand and forecast future stock requirements.

Why is stock control important in warehouse management?
Meeting demand
Effective warehouse management has many aspects, but one of the most important is the ability to keep careful track of inventory by having an effective stock control system in place.
The primary purpose of warehouse stock control is to ensure that there is an adequate supply of products to meet customer demand. Without adequate stock control measures, warehouses can quickly become overwhelmed and disorganised leading to delayed or cancelled orders and dissatisfied customers. Without a clear understanding of what is in stock and what is not, warehouses may become inefficient at managing stock levels, costing time and money.
Stock discrepancies
In addition to meeting customer and supplier demands, stock control helps warehouse managers identify any stock discrepancies early on. Catching these errors before they become a problem is essential for avoiding costly issues such as overstocking, understocking and stock shrinkage. Most retailers and warehouse managers will know that stock shrinkage is very much a problem and can be caused by any number of factors including theft, damage, waste or human error.
Stock control and inventory management is designed to minimise these risks as much as possible by providing immediate data to highlight where stock has been lost and how much.
Pitfalls of not accurately monitoring stock
An example to demonstrate the potential pitfalls of not accurately monitoring stock levels is if an online retailer sends out an email promoting a particular product to boost sales. The promotion works and orders begin coming in. As the warehouse staff start to pick and pack these orders, there is a problem - a whole box of the particular product you believed to be sitting on the shelf is missing. This could have happened for a number of reasons; the last order from the supplier was short, stock wasn’t adequately checked when it arrived, or did sales far exceed the expected number and a reorder is required.
Regardless of the reason, it highlights the importance of sufficient warehouse stock control systems and how issues can arise without them. As well as being able to accurately monitor stock levels and trends to help warehouse managers plan ahead and prepare for upcoming orders, stock control is equally useful in avoiding overordering and creating deadstock inventory that occupies space and loses retailers money.
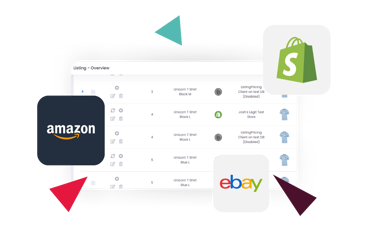
5 Different stock control methods
Having a good stock control system in place is essential for retailers wishing to grow and increase their profitability. There are a variety of different stock control methods, each of which has its own advantages and suitable applications. In this section, we explore a few of the most popular stock control methods.
1. Basic spreadsheet tracking
This is a very simple and cost-effective way of tracking your inventory. All you need is a basic spreadsheet program and all the relevant information about your stock. With this method, you’re able to easily track your orders, deliveries, purchases, and stock levels all in one place. This method, however, isn’t suitable for businesses with complex or large inventory needs, as it can become difficult to manage and update manually.
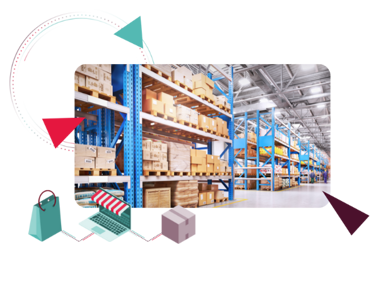
2. Automated ordering systems
Automated ordering systems are an ideal stock control method for businesses that want to streamline their ordering process. Automated ordering systems allow businesses to set certain parameters for when and how to order new stock. When the parameters are met, the system will automatically place the order for you, eliminating the need for manual input. Although this method is relatively easy to set up, there can be a significant cost involved depending on the type of system you use.
3. Barcode scanning inventory systems
Mobile barcode inventory systems are a popular stock control method that uses barcodes to identify and track products. Barcodes contain essential information such as the product’s name, size, quantity, and price. By scanning these codes, businesses are able to quickly and easily keep track of their stock and orders. Additionally, this method is also very cost-effective, as it requires no additional hardware or software and can be done with a simple smartphone or tablet. Discover the benefits of implementing a barcode inventory system in your warehouse.
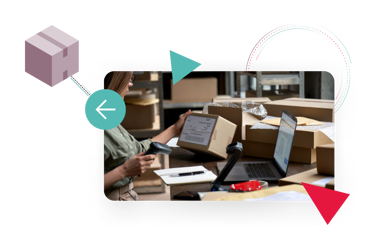
4. Radio-frequency identification (RFID)
Radio-frequency identification is a newer method of stock control that uses radio-frequency technology to track products. RFID tags are attached to each item and contain all the relevant information. This allows businesses to quickly scan entire batches of inventory and track their orders and stock levels. This warehouse stock control method is particularly useful for businesses with complex inventory needs, as it is able to handle large volumes of data more efficiently.
5. Warehouse stock control software
Warehouse stock control software is a great way for businesses and warehouse managers to keep track of their inventory in real-time. This software is usually installed on a cloud-based server and accessed via the internet, allowing businesses to access their data from anywhere and at any time.
Additionally, it also offers integrations with various other pieces of software, such as mobile barcode scanning software and inventory warehouse software. This makes it easy to keep track of multiple aspects of your business at once.

Improve warehouse stock control with best practices
Whilst it is important to choose a warehouse stock control process that fits your business’ size and operation, there are a number of tried and tested solutions that will assist in maintaining an efficient and effective warehouse stock control system.
Set PAR levels or minimum levels of stock
The process of setting PAR levels is similar to forecasting demand levels. To keep good control over your stock, you will first need to establish how much you need and how much you’ll be able to sell. Based on these figures, you should be able to set a PAR level for each product which represents the minimum level of stock you need to have in the warehouse at any given time to be able to fulfil orders.
If inventory falls below this minimum level, you should order more as soon as possible to avoid overselling and experiencing stock shortages. Effective warehouse stock control software should alert warehouse managers when stock reaches the PAR level, allowing them to review and restock.
Setting PAR levels isn’t just about running out of stock, however. If this number is exceeded by too much, warehouse space will be wasted and inefficiencies created. It is therefore important to regularly maintain and review this balancing act to ensure maximum efficiency. Factoring in seasonal trends is important as your PAR level might change over the course of the year.
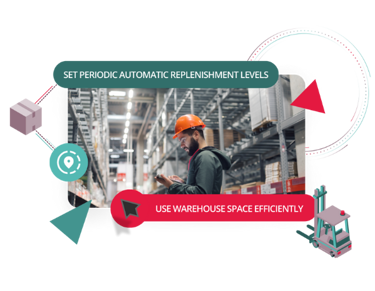
Run an efficient storage and order system
If a warehouse is inefficient, it is likely that stock control processes aren’t particularly thorough either. The best way to ensure that inventory is controlled and managed accurately is to incorporate regular checks and procedures throughout the warehouse supply chain.
This includes:
- Checking stock numbers are accurate upon receival from suppliers - accounting for missing items as soon as possible is essential
- Quality control products to identify issues immediately upon receival
- Proper labelling of stock with individual item codes or SKUs for easy tracking and identification
- Regular stock rotation to avoid expiry or product ageing - this does not only apply to perishable items
- Having clear order forms to reduce the risks of mistake during picking and packing
- Having an accurate returns systems to account for exchanged and returned items
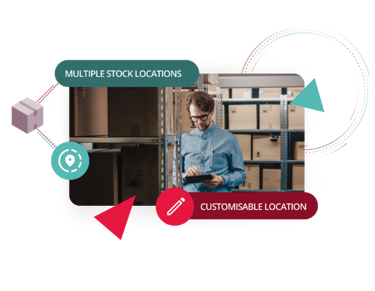
Keep up with stock checks
Stock checks are a simplistic form of stock control, but are still incredibly important. This is the process of physically counting how many of each product sits in the inventory and cross referencing this with records to make sure it matches.
There are a number of stock taking methods including:
- Periodic stock checks - warehouse managers decide how regularly stock needs to be counted e.g. monthly or quarterly and it is then checked in its entirety
- Continuous/cyclical stock taking - Instead of an entire stock check in one go, they are spread out regularly throughout the year, one product line or category at a time
- Spot checking - in between larger stock checks, a product line is chosen to be checked at random to ensure it is selling to plan
- Annual stock take - traditionally done at the end of the financial year when all stock is counted in its entirety
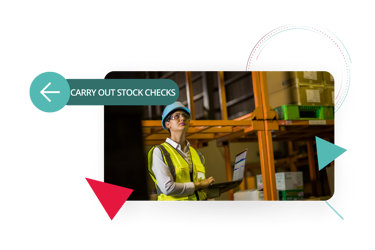
Increase efficiency with a WMS
For a warehouse to perform at its best, a warehouse management system (WMS) is strongly recommended. By using cloud-based warehouse management software, warehouses can benefit from automated workflows, optimised stock control and advanced location management.
With these features in place, warehouse stock control can be easily managed and monitored from one easy-to-use platform that automates many of the manual processes involved in inventory management, allowing your business to rapidly increase its efficiency and stock control accuracy.
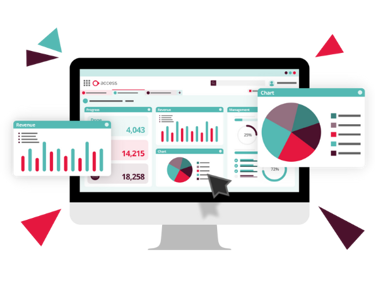
Improve your stock control with warehouse management software
Stock control and inventory management isn’t a small task - it requires continuous maintenance and a high amount of attention to ensure that your warehouse is as efficient and cost-effective as possible. This can be especially difficult for growing or expanding businesses that are struggling to maintain levels of efficiency with their existing stock control systems as they grow.
From mobile barcode scanning to cloud-based warehouse management software, Mintsoft offers a range of software solutions to ensure you are meeting, and exceeding, best practice.
To transform your warehouse stock control, learn more about our warehouse management software or book a 1-1 demo today.
Frequently asked questions
What is stock control in a warehouse?
Stock control is the process of keeping track of how much product a warehouse has and where inventory has gone. This can be done manually or with the help of automated systems.
What are PAR levels?
PAR levels (Periodic Automatic Replenishment) are minimum and maximum quantity limits set for a certain product being stored in a warehouse. When the quantity approaches the minimum level, the item should be reordered.
What are the principles of stock control?
There are five key principles of stock control in inventory management:
- Demand forecasting
- Warehouse flow
- Inventory turns/stock rotation
- Cycle counting
- Process auditing
By incorporating these fundamental principles into warehouse management, businesses can achieve significant cost savings and efficiency.
How can you improve stock control?
Ultimately, to improve the stock control process, you should:
- Perform accurate forecasting
- Highlight high selling products
- Educate staff on how to improve stock control
- Regularly inspect stock
- Maintain a good relationship with suppliers
- Consider inventory optimisation tools such as warehouse management software to automate a lot of processes and improve accuracy
- Make smart decisions about slow moving and obsolete stock
- Resolve issues quickly and effectively